CONVENTIONAL NDT SERVICES PHILIPPINES

Radiographic Testing(RT )
In conventional radiographic testing (RT), a source of X or gamma radiation is used to produce an image of the component on photographic film. It can also be used for other applications like casting and failure analysis. Radiographic Testing (RT)
is a non-destructive examination (NDE) technique that uses X-rays or gamma rays to view the internal structure of a component. This method is highly effective in detecting hidden flaws such as cracks, porosity, slag inclusions, and other volumetric defects within welds, castings, and structural components. RT is particularly valuable for its ability to provide a permanent visual record of the inspection results.
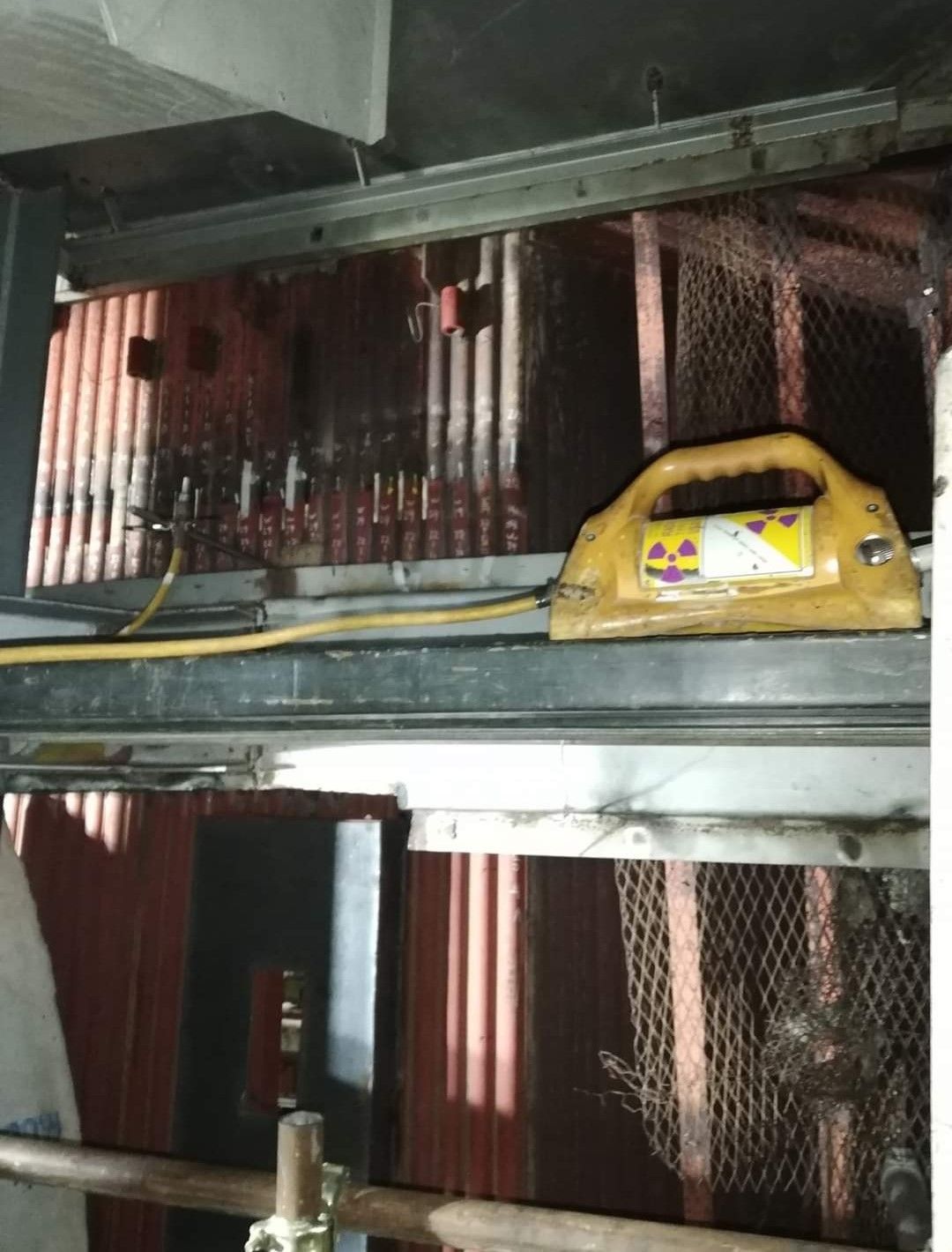

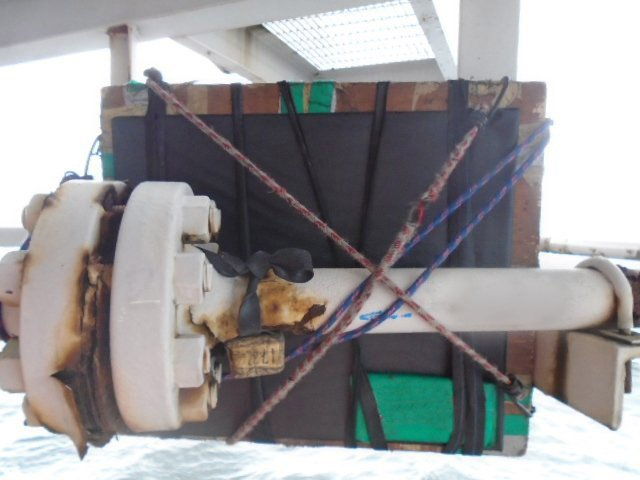

Ultrasonic Testing(UT)
Ultrasonic Testing (UT)
uses high-frequency ultrasonic waves to detect surface breaking and internal imperfections.
Ultrasonic Testing (UT) is a volumetric non-destructive testing method used to detect internal flaws and measure wall thickness in materials.
BIISCORP performs UT on various structures, with a specialization in weld inspection for piping systems, pressure vessels, and structural components.
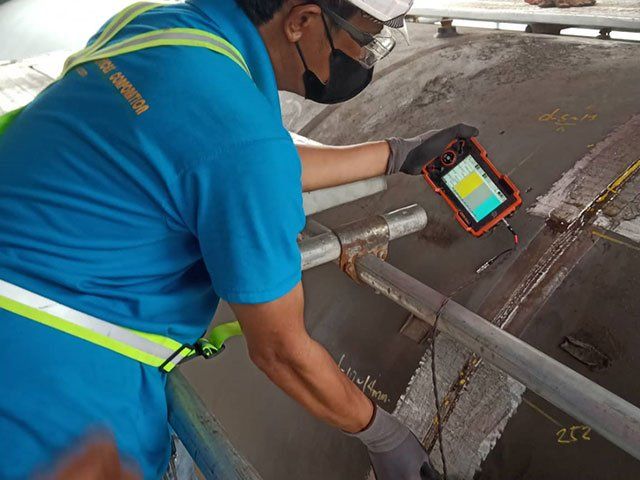

Magnetic Particle Testing(MPT)
The magnetic particle testing (MT) is the (NDT) method used to detect surface and near-surface discontinuities in ferromagnetic materials such as iron, nickel, cobalt, and their alloys.
The process involves magnetizing the test specimen and applying ferromagnetic particles (dry or suspended in a liquid) to the surface. Discontinuities in the material cause distortions in the magnetic field, which attract the particles and form visible indications of flaws such as cracks, seams, laps, or inclusions.
Dye Penetrant Testing(DPT)
The Dye penetrant
examination method is an effective means for detecting discontinuities in non-porous metals and other materials.
Dye Penetrant Testing is a widely used non-destructive testing (NDT) method for detecting surface-breaking defects in non-porous materials. The process involves applying a liquid penetrant to the surface of the component, allowing it to seep into any cracks or discontinuities. After a suitable dwell time, the excess penetrant is removed and a developer is applied to draw the penetrant out of the flaws, creating a visible indication.
This technique is highly effective for detecting surface cracks, porosity, laps, seams, and other discontinuities in materials such as metals, ceramics, plastics, and glass.
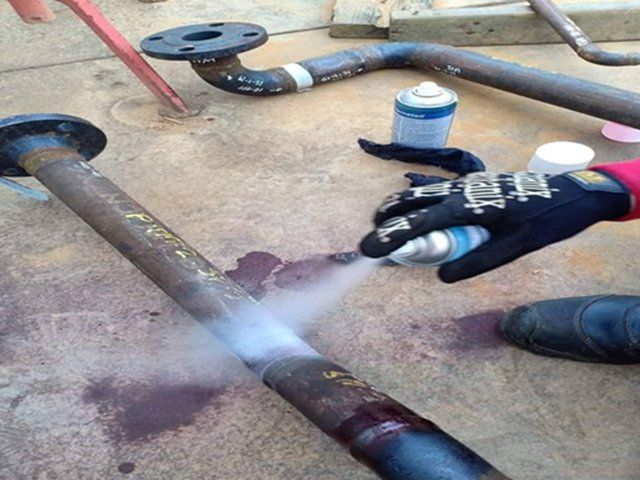

Vacuum Testing(VT)
Vacuum Testing
is a non-destructive testing method used primarily to detect leaks in weld seams or plate joints on non-porous materials. The process involves applying a vacuum box over the test area while a soap solution is applied. If there is a leak, bubbles will form inside the box, indicating a defect.
This technique is particularly effective in detecting through-thickness discontinuities such as pinholes, lack of fusion, or porosity in welds — especially in tank floors, storage vessels, and pressure-retaining components.
Visual Inspection(VI)
Visual Testing
is the most fundamental and widely used non-destructive testing (NDT) method. It involves the direct observation of surfaces to detect discontinuities such as cracks, corrosion, misalignment, weld defects, and other surface irregularities.
This method often serves as the first step in the inspection process and can be enhanced with the use of tools such as magnifying glasses, borescopes, mirrors, cameras, and drones.
Inspections are conducted by qualified personnel following standardized procedures, often supported by calibrated lighting and photographic documentation for accurate reporting and traceability.
Visual Inspection of Boom Crane in FPSO facility.
This purpose is to find out the external condition of the boom crane prior to repair at the selected location. The visual inspection revealed multiple holes in the boom crane. This method of application could direct or remote visual inspection.
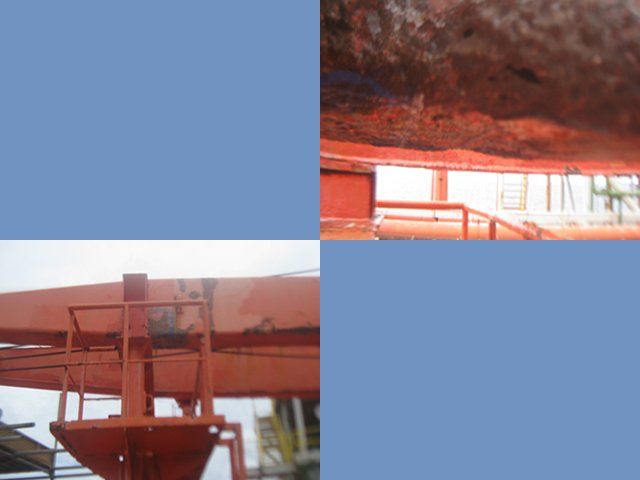

Risk Based Inspection(RBI)
Risk-Based Inspection (RBI)
is a systematic and data-driven approach to planning and prioritizing inspection activities based on the risk of equipment failure. It combines the likelihood of failure (based on degradation mechanisms, operating conditions, and historical data) with the potential consequences (such as safety hazards, environmental impacts, or economic losses) to optimize inspection resources and ensure asset integrity.
RBI
enables plant operators and asset managers to shift from time-based to risk-informed strategies, focusing efforts where they matter most — reducing unnecessary inspections, minimizing downtime, and improving safety and reliability.